Welding to a cast iron manifold, and some stainless
#1

OK whole bunch of pics. First some cast iron welding on a stock cast iron turbo manifold, and then some pics from the latest header batch.
A guy wanted to add an external gateto his stock turbo manifold. Now i am not a huge fan of this setup, but I decided to try it because I happened to have an old manifold laying around and I wanted to try welding some cast iron.
The cast manifold welding question gets asked a bit, and this method worked extremely well for me, I ain't the ultimater welde or anything but maybe this will help.
As some of you may know cast iron is a tricky material to weld - it has a very high carbon content (especially cooked old exhaust manifolds) and as the welds cool it will not "give" as the welds shrink and it cracks.
To make things more difficult this manifold has some cracks that went right through:
Here is an example:

So, die grinder with a carbide burr abd "vee" them out:


Then we weld them using using TIG. I am using a 3/32" pure nickel rod (NI99) and around 120 amps I guess. No preheat. No postheat. I ran 1" of weld, and allowed it to cool naturally until it was cool to the touch. Time consuming but I just work on other stuff while it cools.
So I ran the one pass straight in the VEE, basically a root pass. Once that was done I did a bdit of grinding here and there as there was a bit of porosity in a couple of spots.
Then I ran a weave/cap at around 100amps:
I ran that over all of the cracks as well.
As far as the NI99 goes- it runs OK. Welding cast iron is weird, it's kinda... "lumpy". It's a good quality casting though from what I can tell.
I noticed I have no decent pics of where I welded the pipe to the manifold, or the hole in the manifold itself becuase I guess I am a tool. I'll take some tonight.
Here is one weird pic of the hol machined in the header and where I laid some nickel filler around the edge, run fairly cold just to kind prep the material.
Then I burned the pipe onto the hole:

Here is the one pic I found of welding the pipe to the manifold, this was dfone in 2 passes as well, this is just the first one (nickel rod still- notice this is welded to cast and shows no sign of any crackinf at the end of the weld):

I used schedule 40 steel pipe for this, rather than stainless. It's a long piece of pipe with quite a bit of load on it so I decided that thickwall would be better.
The pipe needs a LOT of cleaning to weld very well with TIG- it seemed to have a lot of oil on/in it.
Anyways I welded the pipe in 2 passes- one root pass at around 130amps with almost no filler then a cap at aroun 80-100 amps, here you can see the root pass with the cap going on top:

Finished weld, a little hot/undercut, etc but it'll do:

Here is a pic of the inside, you can see at the bottom where I got a little hot an almost dropped through. Overall, fairly decent underside, good solid 100% penetration right through:

And here's a horrible pic what it'll look like, I have to just weld the pipe onto the "stub" piece of pipe I welded to the manifold, I'll take better pics tonight:

Anyways all in all the nickel rod+ stronger works good! I had no cracking issues at all.
A couple from the latest header round:





More tonight.
A guy wanted to add an external gateto his stock turbo manifold. Now i am not a huge fan of this setup, but I decided to try it because I happened to have an old manifold laying around and I wanted to try welding some cast iron.
The cast manifold welding question gets asked a bit, and this method worked extremely well for me, I ain't the ultimater welde or anything but maybe this will help.
As some of you may know cast iron is a tricky material to weld - it has a very high carbon content (especially cooked old exhaust manifolds) and as the welds cool it will not "give" as the welds shrink and it cracks.
To make things more difficult this manifold has some cracks that went right through:
Here is an example:

So, die grinder with a carbide burr abd "vee" them out:


Then we weld them using using TIG. I am using a 3/32" pure nickel rod (NI99) and around 120 amps I guess. No preheat. No postheat. I ran 1" of weld, and allowed it to cool naturally until it was cool to the touch. Time consuming but I just work on other stuff while it cools.
So I ran the one pass straight in the VEE, basically a root pass. Once that was done I did a bdit of grinding here and there as there was a bit of porosity in a couple of spots.
Then I ran a weave/cap at around 100amps:

I ran that over all of the cracks as well.
As far as the NI99 goes- it runs OK. Welding cast iron is weird, it's kinda... "lumpy". It's a good quality casting though from what I can tell.
I noticed I have no decent pics of where I welded the pipe to the manifold, or the hole in the manifold itself becuase I guess I am a tool. I'll take some tonight.
Here is one weird pic of the hol machined in the header and where I laid some nickel filler around the edge, run fairly cold just to kind prep the material.
Then I burned the pipe onto the hole:

Here is the one pic I found of welding the pipe to the manifold, this was dfone in 2 passes as well, this is just the first one (nickel rod still- notice this is welded to cast and shows no sign of any crackinf at the end of the weld):

I used schedule 40 steel pipe for this, rather than stainless. It's a long piece of pipe with quite a bit of load on it so I decided that thickwall would be better.
The pipe needs a LOT of cleaning to weld very well with TIG- it seemed to have a lot of oil on/in it.
Anyways I welded the pipe in 2 passes- one root pass at around 130amps with almost no filler then a cap at aroun 80-100 amps, here you can see the root pass with the cap going on top:

Finished weld, a little hot/undercut, etc but it'll do:

Here is a pic of the inside, you can see at the bottom where I got a little hot an almost dropped through. Overall, fairly decent underside, good solid 100% penetration right through:

And here's a horrible pic what it'll look like, I have to just weld the pipe onto the "stub" piece of pipe I welded to the manifold, I'll take better pics tonight:

Anyways all in all the nickel rod+ stronger works good! I had no cracking issues at all.
A couple from the latest header round:





More tonight.

#3

good work! CI is inconsistant, loaded with impurities and ni isn't the easyest thing to tig!

Falling throgh too hot? Na, you kidding you just hit proper heat and root reinforcement LoL! Maybe a hair much in that big glob, but it's definately within spec, and in a perfect world would only be say 1/32"-1/16" lower. Reinforcement height = the radious of the rod is a great thing to shoot for on these smaller pipes =) (aslong as it's no more than 1/8" high - obviously in our kind of welding you'd want >/=1/16")
Try and do that all the way around next time!

Falling throgh too hot? Na, you kidding you just hit proper heat and root reinforcement LoL! Maybe a hair much in that big glob, but it's definately within spec, and in a perfect world would only be say 1/32"-1/16" lower. Reinforcement height = the radious of the rod is a great thing to shoot for on these smaller pipes =) (aslong as it's no more than 1/8" high - obviously in our kind of welding you'd want >/=1/16")
Try and do that all the way around next time!
#4

Thanks guys,
Toys,
part of the difficulty with the steel pipe was that as strange as it may sound, I almost never weld mild steel these days, all stainless and aluminum - so I set up to weld and realized the only mild steel tig rod I had hiding anywhere in the shop was -.045".
Welding almost 1/4" thick with 0.045" was a bit awkward. I would have used 3/32" if I'd had some.
And yeah, I was suprised and how inconsistent the steel for schd 40 was. Some of it is my fault though- come to think of it I was pretty lazy when I beveled the pipe and it could have been a more even bevel- part of why the penetration is inconsistent I think- it seems a pretty small change in the geometry of the root gap will change the weld profile a LOT. Things to keep in mind for next time (not that I plan on welding lots of retarded wastgate pipes on to stock manifolds!)
I love learning though and I learned a lot doing this.
Tcel,
This is all Volvo 8v 2.3L ----.
The torch is a CK Flex-Loc. The head of the torch can be rotated for access. It's really nice for collectors and such. The only thing that sucks is I with I had bought a watercooled one. I never had issues with the torch getting hot back when I was a major noob because I could only weld a little bit without having to reposition, fix the fucked up tungsten, etc. Now I am aboutr speed. When I am on a project I want to get the ********** DONE- I don't mean do a shitty job just to get it done, I just mean the torch hetaing up is limiting how quickly I can work.
I finished it last night and got some pics of the actual weld joint to the manifold and the completed manifold. As I mentioned before it is kindof a retarded design but it's how the guy wanted it.

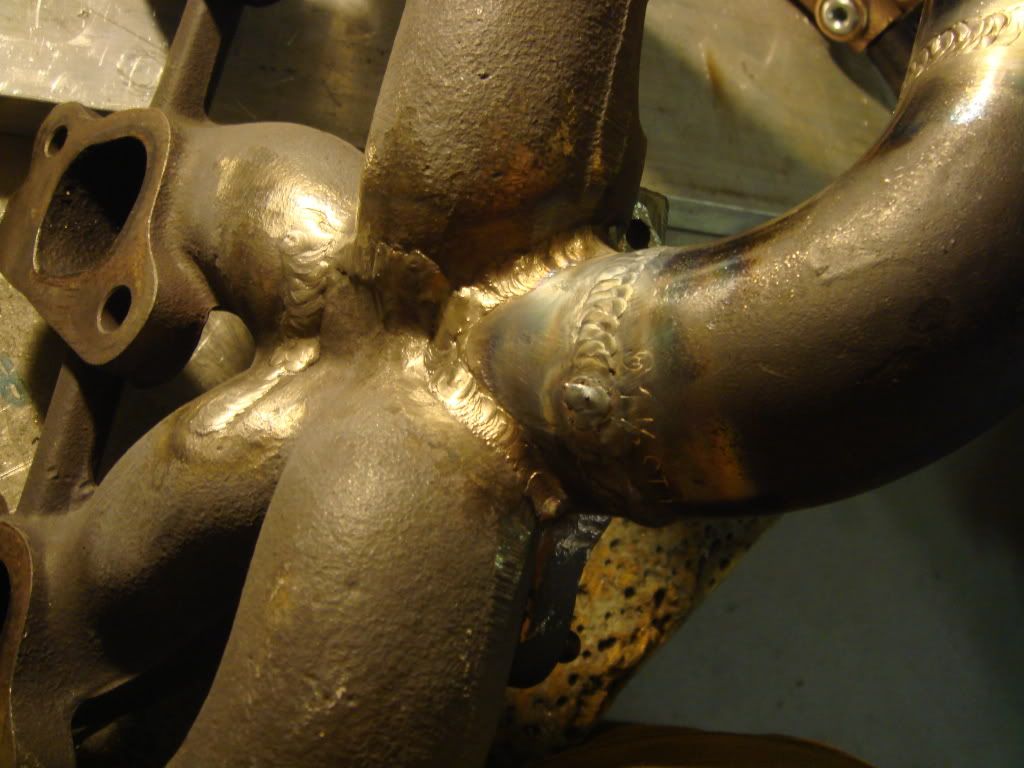

I have a few more of the "standard" stainless headers to make, then a 0.065" one from 321 (customer insisted
).
The I am redoing my really shitty 6 cylinder manifold. Got a new T67 with w twin scroll T4 turbine housing- so I am looking forward to that. It's going to be a beast of a manifold.
Cheers guys!
Toys,
part of the difficulty with the steel pipe was that as strange as it may sound, I almost never weld mild steel these days, all stainless and aluminum - so I set up to weld and realized the only mild steel tig rod I had hiding anywhere in the shop was -.045".

Welding almost 1/4" thick with 0.045" was a bit awkward. I would have used 3/32" if I'd had some.


Tcel,
This is all Volvo 8v 2.3L ----.

The torch is a CK Flex-Loc. The head of the torch can be rotated for access. It's really nice for collectors and such. The only thing that sucks is I with I had bought a watercooled one. I never had issues with the torch getting hot back when I was a major noob because I could only weld a little bit without having to reposition, fix the fucked up tungsten, etc. Now I am aboutr speed. When I am on a project I want to get the ********** DONE- I don't mean do a shitty job just to get it done, I just mean the torch hetaing up is limiting how quickly I can work.
I finished it last night and got some pics of the actual weld joint to the manifold and the completed manifold. As I mentioned before it is kindof a retarded design but it's how the guy wanted it.

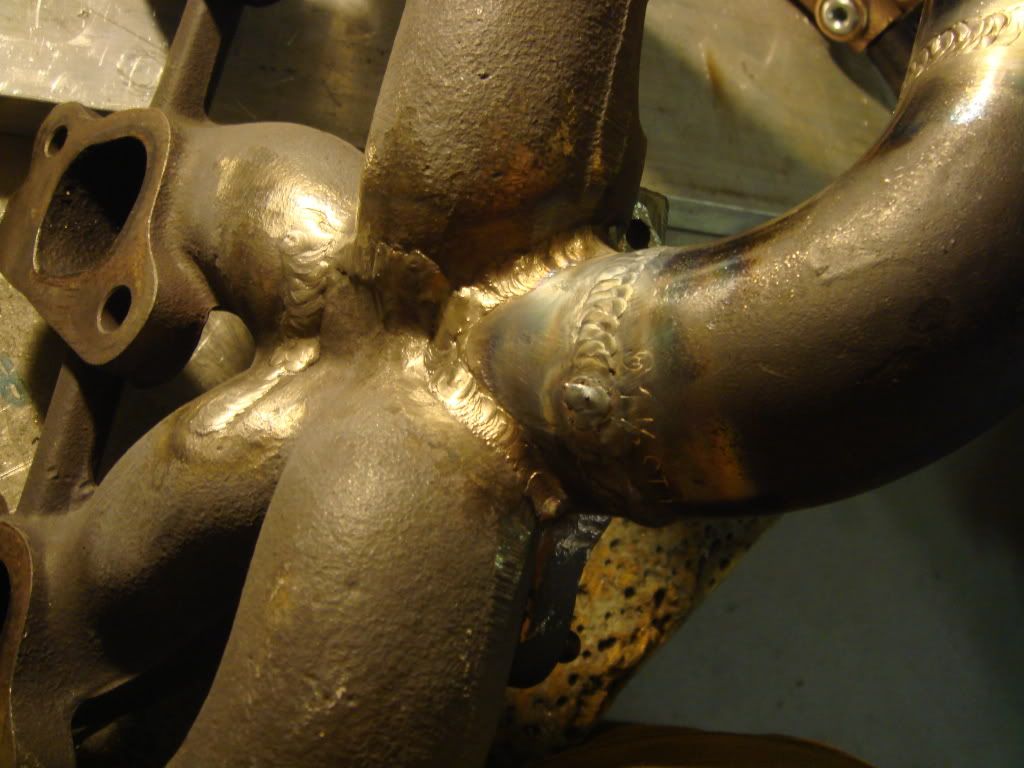

I have a few more of the "standard" stainless headers to make, then a 0.065" one from 321 (customer insisted

The I am redoing my really shitty 6 cylinder manifold. Got a new T67 with w twin scroll T4 turbine housing- so I am looking forward to that. It's going to be a beast of a manifold.

Cheers guys!
#5

i've only welded cast once, used my trusty HF flux-crore on high heat slow feed.
just welded a MS flange to it, never cracked. welds looked like ---- though because i barely prepped it, and it was my 3rd time ever welding anything
just welded a MS flange to it, never cracked. welds looked like ---- though because i barely prepped it, and it was my 3rd time ever welding anything
#6

I've heard of a few people doing that- I think that many (probably not all of course) exhaust manifolds seem to be pretty good quality castings and have a fair amount of nickel in them already, which helps. I tried to weld a broken cast iron
Fluxcore sure would have been faster.

Fluxcore sure would have been faster.


#7

they actualy make a stick welding rod made just for cast iron , in a few differint sizes too ! easy to use and if you clean each weld really good , multi passes almost never crack or have any seperation from surrounding material as would just about any other rod . just a good piece of info for welding / modifying stock manifolds .
#10

ok so i thought it was about tig welding cast ? i was just sayin there is also a Stick welding rod for cast welding ....... but i guess everyone here already knew that for a very very long time .. ---- me for throwin in some info that possibly somone els could use .